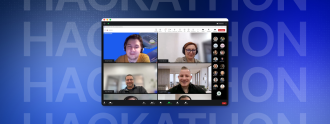
Contact us
Our team would love to hear from you.
Empowered by data analytics, human–machine interaction, automation, and connectivity, the Fourth Industrial Revolution has paved the way for smart manufacturing and is radically transforming how companies produce and deliver their products. In this article, we trace what has laid the foundation for Industry 4.0 and delve into the essence of this breakthrough, shedding light on its associated technologies, benefits, and potential impact on global business.
The 4th Industrial Revolution has gained momentum in the second decade of the 21st century and is a natural progression of the first three industrial revolutions.
The First Industrial Revolution, spanning from 1760 to 1840, was a turning point in human history. It was distinguished by the invention of the steam engine, which reduced reliance on human and animal labor and mechanized some production processes.
The Second Industrial Revolution, also known as the Technological Revolution, occurred between 1870 and 1914. It was characterized by the advent of electricity and multiple technological advancements such as the assembly line, ushering in a new era of mass production.
The Third Industrial Revolution, or the Digital Revolution, marked its presence in the 1950s with the introduction of computers and further progressed with the invention of the Internet and digital technologies. Finalized in 2015, the Digital Revolution led to the increasing automation of manufacturing processes and ultimately gave rise to the next technological revolution, now known as Industry 4.0.
The Fourth Industrial Revolution, also called Industry 4.0 or 4IR, builds upon the completed digitization process and involves the integration of advanced technologies during production operations. While it is primarily focused on manufacturing, Industry 4.0 affects every business segment of the global economy with its ultimate goals being:
Innovative technologies, such as big data, artificial intelligence (AI) and machine learning (ML), robotics, blockchain, the Industrial Internet of Things (IIoT), and cloud computing, are the major drivers behind Industry 4.0. These same technologies also underpin the development of smart manufacturing and smart factories, which are at the core of the Fourth Industrial Revolution.
Smart manufacturing involves leveraging powerful technologies to connect machines, people, and processes to optimize operational performance and streamline product manufacturing. The physical manifestations of this concept are digitized manufacturing facilities, known as smart factories.
Smart factories act as cyber–physical systems (CPS) that use interconnected equipment, application integration, and smart technologies to exchange and analyze real-time data and drive automation and human–machine interoperability in production operations. Such systems help businesses extract invaluable insights from historical data, enable automated decision-making, predict market trends and fluctuations, and respond to ever-changing customer demands while fostering efficiency and improving financial performance.
The 4th Industrial Revolution achieves its full potential by leveraging the following technologies:
The IIoT, a central element of any smart factory, is the use of the Internet of Things (IoT) for industrial purposes. The IIoT forms a responsive ecosystem of all assets on the shop floor equipped with sensors to enable their communication and the exchange of real-time data. Harnessing IIoT technology helps businesses monitor equipment performance, minimize downtime, and identify malfunctions, optimizing overall productivity and ensuring smooth supply chains.
AI and ML empower smart manufacturing by capturing and analyzing large sets of data not only from IoT-enabled devices but also across various business areas and third-party sources. AI and ML help companies recognize complex data patterns and generate insights based on these patterns, enabling data-driven decision-making. AI and ML also deliver additional benefits to businesses, including the ability to implement predictive maintenance strategies, identify opportunities for improvement, and streamline business operations.
As one of the critical Fourth Industrial Revolution technologies, robotics focuses on creating and operating physical robots powered by AI and typically equipped with modern software, sensors, and machine vision. Robotics technology provides extensive manufacturing capabilities by increasing the automation of complex and repetitive assembly line tasks and contributing to the data collection process. Employing this technology in manufacturing translates into improved productivity, cost efficiency, and flexibility, which fully aligns with the objectives of Industry 4.0.
3D printing, or additive manufacturing, is a fundamental aspect of Industrial Revolution 4.0 that involves creating three-dimensional solid objects from digital models. Leveraging 3D printing in production processes allows for rapid prototyping of industrial products, empowers on-demand custom manufacturing, accelerates design iterations, and streamlines multiple manufacturing operations. Consequently, this valuable tool minimizes waste, saves production costs, and significantly reduces the impact of manufactured products on the environment.
One of the pillars of Industry 4.0, AR merges the physical and digital worlds by enhancing a real-world environment with digital visual elements, sounds, and other sensory input. Applications of AR in production processes vary widely, ranging from product development and maintenance to employee training and quality control. Using AR in production operations offers numerous benefits, including improved product quality, simplified maintenance processes, refined employee skills, increased work safety, and more.
The technology revolution in question would not have gained traction without cloud computing. This disruptive tool fuels other prominent technologies, such as A, and provides a scalable and cost-efficient infrastructure for managing large volumes of data generated by IoT devices. Cloud software solutions help businesses efficiently store, process, and analyze their data in real time while significantly minimizing costs, making it the most leveraged Industry 4.0 technology, with 85% of manufacturing businesses having adopted it thus far.
Cutting-edge digital twin technology is an indispensable element of Industry 4.0. It uses AR, 3D graphics, and data modeling to build a virtual replica of a product, process, service, or system to simulate its behavior in real time and predict how it will perform before it goes into production. With digital twin technology, manufacturing companies can quickly and easily identify potential issues, streamline manufacturing operations, increase equipment reliability, and expedite the entire production process.
Traditional databases pose an increasing number of challenges when handling transactions and data, so manufacturers are shifting towards capitalizing on blockchain technology. As a decentralized and distributed ledger technology akin to a database, blockchain is used to securely store data in a chain of linked blocks for further data recording, sharing, and traceability. Manufacturing enterprises leverage this advanced technology to streamline business operations, increase supply chain visibility, track interactions with suppliers and business partners, enhance data security, and more.
The Fourth Industrial Revolution goes far beyond technology upgrades. By unifying people, machines, and operations, Industry 4.0 initiatives help business owners develop a more holistic approach to manufacturing, transforming the entire product lifecycle along with its supply chain and making products more accessible to consumers. Other compelling 4IR benefits are outlined below.
Smart manufacturing and smart factories associated with Industry 4.0 automate multiple manufacturing operations, creating self-optimizing production systems capable of decentralized decision-making. These intelligent systems reduce machinery downtime, identify operational bottlenecks, and drive overall equipment effectiveness (OEE) and improved maintenance, which translates into increased efficiency and higher production output.
By taking full advantage of the technologies, strategies, and tools of the Fourth Industrial Revolution, such as 3D printing, data management, advanced analytics, and system integration, businesses can significantly enhance the quality of their products while reducing operational and maintenance costs. Improved product quality results in better customer experiences, driving customer spending and boosting companies’ revenues.
Manufacturing 4.0 propels the achievement of sustainable development due to the use and convergence of intelligent Industry 4.0 technologies. This technology-driven approach minimizes waste, reduces material and energy usage, and enables efficient resource allocation throughout the production line, significantly reducing the ecological footprints of companies without sacrificing their efficiency and manufacturing output.
Traditional factory facilities typically function in silos, resulting in minimum collaboration between departments, employees, and machines. Industry 4.0 technologies effectively break down operational silos by enabling communication and real-time data transmission between standalone devices and systems, facilitating collaboration between various departments and even factories regardless of their location or time zone.
Boosting profitability is one of the primary reasons business stakeholders across various domains adopt the latest technologies and adhere to 4IR strategies. Production efficiency, improved product quality, reduced production and labor costs, and minimized waste during manufacturing operations all lead to optimal business outcomes and higher profit margins.
The Fourth Industrial Revolution is having a significant impact on global business, shaping its future trajectory and long–term development. As a result of increased automation, nearly 800 million employees worldwide will lose their jobs by the end of 2030. At the same time, 4IR smart technologies will give impetus to the emergence of millions of new jobs across various industries and domains.
Industry 4.0 technologies will enable efficient production, resulting in cut–throat competition among businesses. Companies will reduce the costs of their products and services to attract new customers and retain existing ones. In addition to delivering products and services, manufacturers will focus on providing frictionless customer experiences with personalized offers to respond to unique and evolving customer needs and foster brand loyalty.
The Fourth Industrial Revolution will ultimately empower the digital transformation process, involving a complete restructuring of all business aspects and cultivating digital cultures.
Game-changing digital technologies, such as the IIoT, AI and ML, blockchain, robotics, and cloud computing, and their broad adoption in manufacturing facilities have heralded the era of the Fourth Industrial Revolution. Built upon the inventions of the previous three industrial breakthroughs, Industry 4.0 is disrupting not only the way modern industrial companies operate but also the way people live, work, and interact with the environment. Despite being in its initial phase, 4IR has already benefited numerous manufacturing businesses and laid a solid foundation for the acceleration of the digital transformation process.
At EffectiveSoft, we understand the importance of 4IR technologies for manufacturing businesses, as well as the challenges associated with incorporating such technologies into production processes. Our expert developers have all the necessary competencies to help companies harness the power of intelligent Industry 4.0 technologies and easily overcome emerging business challenges. Contact us now to achieve the best possible outcomes for your business!
Our team would love to hear from you.
Fill out the form to receive a consultation and explore how we can assist you and your business.
What happens next?